
D5 proposes update to oil-change system
to improve safety, enhance efficiency
Using a local Blackfoot company to replenish mechanical fluids used by the district for oil changes will improve safety and efficiency, and a new storage system using clear plastic totes will aid in determining product levels.
All fluids currently used in the D5 shop are stored in 55-gallon drums and dispensed either through a pneumatic-pumping system or in a gravity feed system (pictured directly below).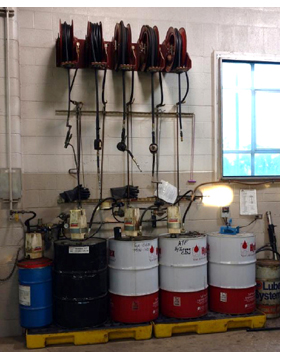
Fluids are purchased from supply in Pocatello, requiring personnel from the shop to drive to their location, where the drums are loaded in the back of the pickup via a forklift. Upon return to the shop, the drums are unloaded using a clamp mechanism to hold the drum (pictured at right) and an overhead crane to lift it out of the pickup and stage next to the storage drums.
Normally this is a two-person job for the sake of safety, but occasionally the workload in the shop dictates that a lone employee perform the task.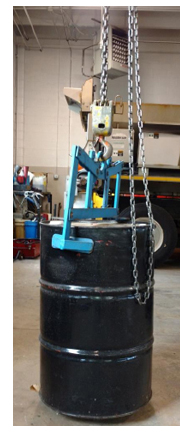
Fluids are transferred to the drums in the shop from the purchased drum via a pump. The entire process takes at least two and a half hours.
The empty drums have to be stored in the shop until a trip is made to Pocatello to pick up full drums, which can add to the confusion of knowing which are full and empty.
Using the current metal drum system also means the volume of oil available at any given time is essentially unknown. When changing the oil in a vehicle, there is sometimes not enough product to finish the job — but that is not known until the job has started, requiring the work to be stopped temporarily while a trip is made to secure more oil.
This is a very inefficient use of shop personnel time, and can be extremely frustrating.
In addition, the safety of personnel unloading the drums and moving them to the staging area could be improved. There is a potential that the clamp could slip off the drum when it is lifted out of the pickup or being moved to the staging area. The overhead crane is manually operated to lift the drum and then it has to be pushed by the employee to move out of the pickup and to the staging area.
In accordance with recent efforts to implement the 5-S program, there exists a potential to improve visibility, clearly identify the fluid, and improve the cleanliness of the shop area.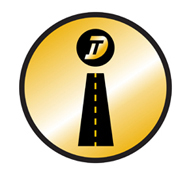
The proposed tote storage system is made up of square plastic totes (pictured directly above) that range in size from a 75-gallon to 330-gallon capacity. They can be organized on a stand, then stacked and organized. The current pneumatic-dispensing pumps can be used with the totes, requiring no additional expense. Local vendors rent or sell the totes to the state for a minimal charge, and fill them on a regular schedule to insure adequate product remains on hand. The vendor maintains the totes and takes care of any needed repairs.
Times 7 Focus: Ideally, these innovations will not live in a silo — they will be catalysts for ITD's other district offices and work areas, and inspire duplication statewide. These innovations represent time and money-saving measures, process improvements, and customer-service efficiencies that are transferrable to other districts. In that spirit, if this innovation is something you'd like to adapt to your own district or work space, and you have any questions, please contact District 5 Innovation Steward Greydon Wright at 5-3317.